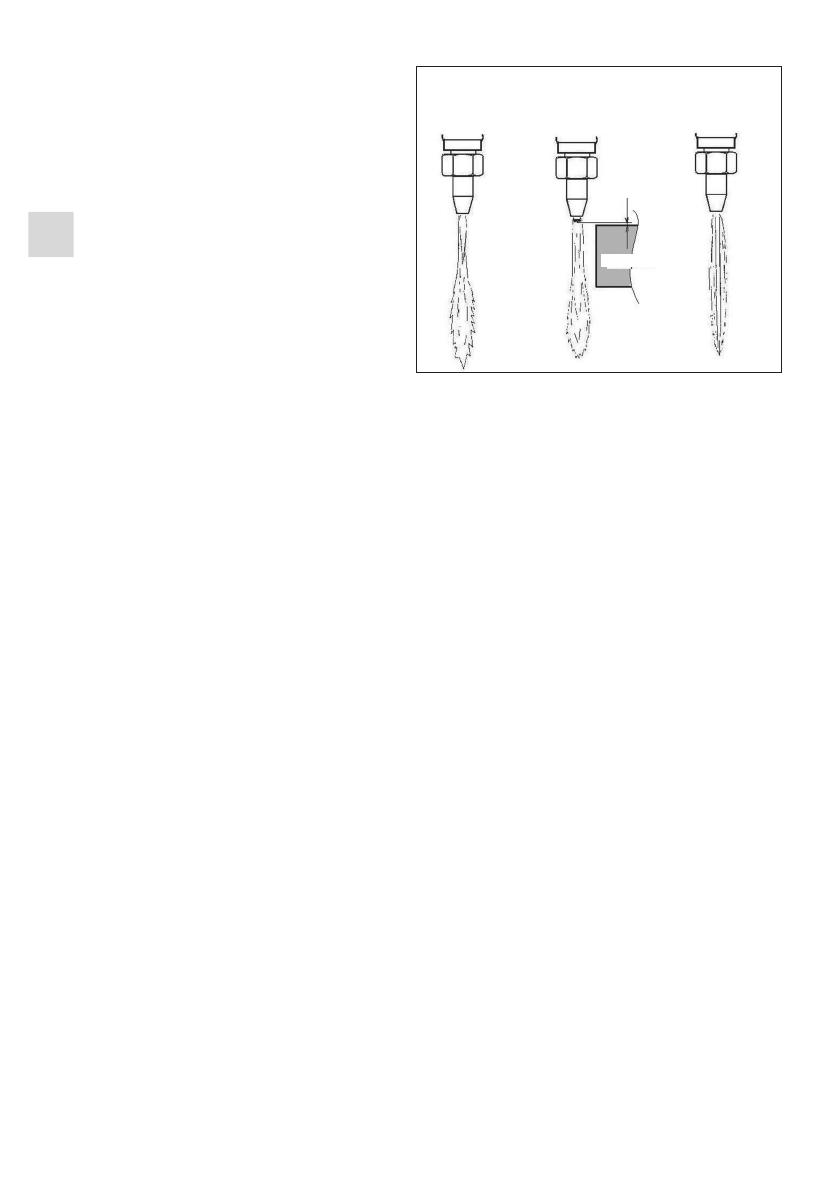
DE
20/136
4. BETRIEB
4.1. VOR DEM SCHNEIDEN
4.1.1. Das Bedienpersonal muss vor
der Inbetriebnahme der ProFIT® SLM
Maschine mit den Grundsätzen der
Arbeitssicherheit vertraut sein, die in
dieser Bedienungsanleitung genannt
sind, und. Das Bedienpersonal muss
Erfahrungen mit dem Brennschneiden
haben und gemäß den Anforderungen
aus den ISO, EN Normen sowie den na-
tionalen gesetzlichen Vorschriften und
Verordnungen unterwiesen sein.
4.1.2. Es sind nur die Schneiddüsen
gemäß der oben angegebenen Tabelle
zu verwenden. Die Gasart ist entspre-
chend zu beachten. Verwenden Sie nur
einwandfreie und unbeschädigte Düsen mit unbeschädigtem und sauberem Sitz.
4.1.3. Kontrollieren Sie auch den Sitz des Schneidbrennerkopfs vor der Montage der
Schneiddüse. Nur ein Schneidbrenner gemäß der oben angegebenen Typen darf verwendet
werden. Die Gasart ist zu beachten.
4.1.4. AUSWAHL DER SCHNEIDDÜSE
Gehen Sie gemäß der oben angegebenen Tabellen für die jeweilige Schneiddüse vor.
Wenden Sie die richtige Düsengröße gemäß der Materialdicke an. Die GCE Schneiddüsen
sind für Schnitte auf dem Qualitätsniveau 1 gemäß der Norm EN ISO 9013 vorgesehen. Die
maximale Schneidgeschwindigkeit für Geradschnitte kann nur durch die Einstellung der
Schneidparameter gemäß der oben angegebenen Tabelle, unter Berücksichtigung sauberer
Blechoberflächen, einer intakten Brennschneidmaschine, mit unbeschädigter Schneiddüse
und einer Sauerstoreinheit von mind. 99,5% oder mehr erreicht werden. Die Gasdruckwerte
werden am Brennereingang gemessen.
4.1.5.ANZUGSMOMENT DER DÜSEN:
Schneidbrenner mit der Mischdüse: 22-30 Nm
Schneidbrenner BIR+: 12 Nm für die innere Schneiddüse und 18Nm für die äußere rmedüse
ANMERKUNG: Alle Bauteile im Kontakt mit Sauersto müssen öl- und fettfrei sein.
Explosionsgefahr! Kontrollieren Sie, ob alle Gewindeverbindungen und Dichtungsoberflächen,
z.B. Kegel und Kugelflächen, sauber und unbeschädigt sind!
4.2. FLAMMENZÜNDUNG UND EINSTELLUNG
4.2.1. Kontrollieren Sie die Dichtheit aller Gasverbindungen.
4.2.2. Stellen Sie die Gasdrücke gemäß den Werten in der oben angegebenen
Schneiddüsentabelle ein, siehe Punkt 2.4. (1 bar = 105 Pa, 100kPa = 105 N/m2, 1 bar = 14,5
psi).Önen Sie das Brenngasventil ca.3/4 Umdrehung und das Heizsauerstoventil ca. ½
Umdehung. Zündern Sie das Gasgemisch mit einem geeigneten Anzünder (Verwenden Sie kein
heißes Metall, Streichhölzer oder Feuerzeuge). Bei der richtigen Druckeinstellung kommt es
zur Bildung einer brenngasüberschüssigen Flamme. Mittels Brenngas- und Heizsauerstoventil
muss die neutrale Flamme so eingestellt werden, dass sie der vorgesehenen Schneidaufgabe
entspricht. Für das Zünden der Flamme verwenden
4.2.3. Önen Sie kurz das Schneidsauerstoventil, damit Sie die richtige Einstellung der
neutralen Flamme sehen, und dann schließen Sie es (siehe auch Bild 4)
Bild 4: Flammeneinstellung
Reduktionsflamme
während des
Zündverfahrens
Neutrale
Flamme
Neutrale Flamme
mit Schneidsau-
ersto
ungefähr 1mm
Arbeitsteil