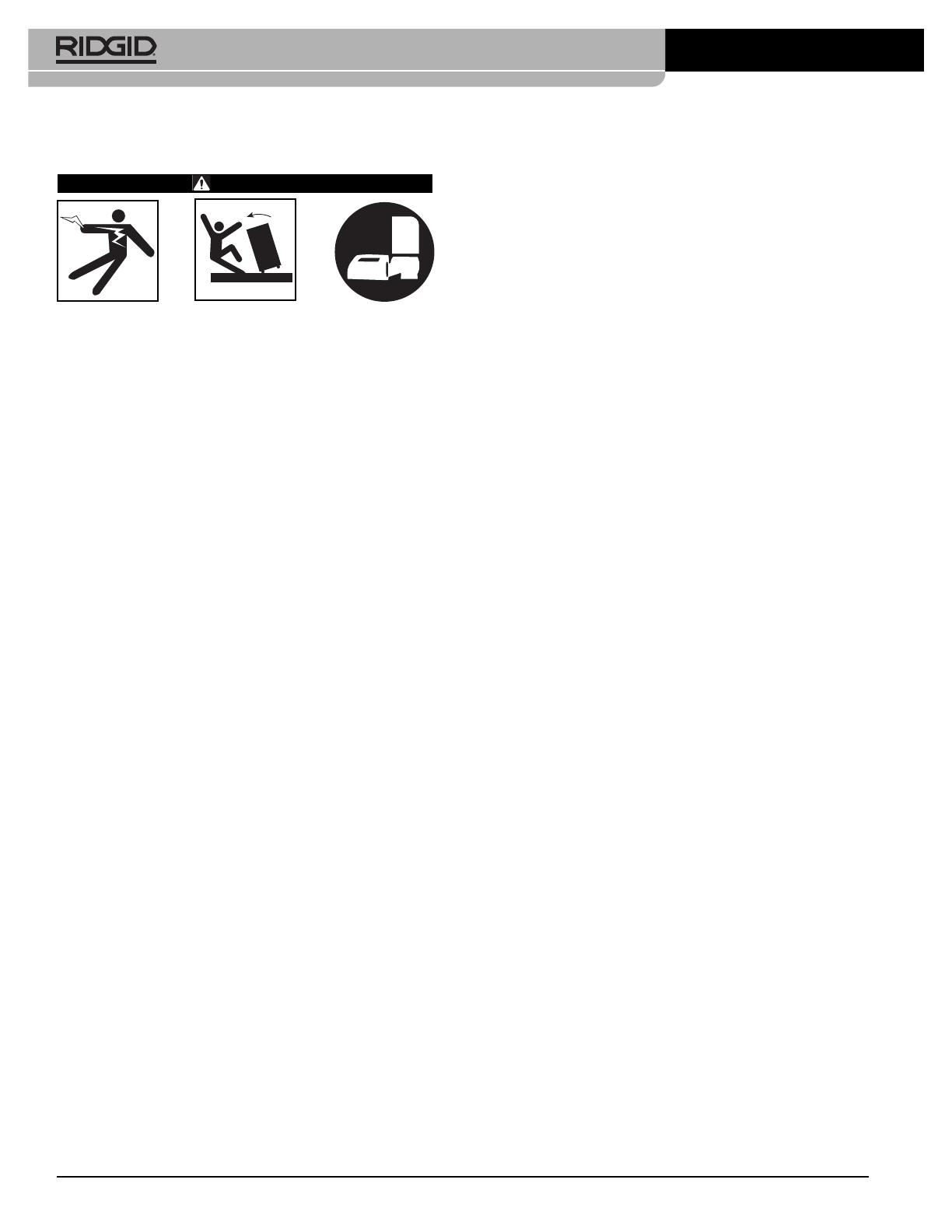
999-998-086.09_REV. C8
535 Manual Chuck/535 Auto Chuck Threading Machines
the die head. See Die Head Set-Up and Use section
for details.
7. Swing the cutter, reamer and die head up away from
the operator. Make sure they are stable and will not fall
in the work area.
8. If pipe will extend past the chip tray in the front of the
machine or more than 4' (1,2 m) out of the rear of the
machine, use pipe stands to support the pipe and pre-
vent the pipe and threading machine from tipping or
falling. Place the pipe stands in line with machine
chucks, approximately 1/3 of distance from end of the
pipe to the machine. Longer pipe may need more than
one pipe stand. Only use pipe stands designed for
this purpose. Improper pipe supports or supporting
the pipe by hand can cause tipping or entanglement
injuries.
9. Restrict access or set-up guards or barricades to
create a minimum of 3' (1 m) clearance around the
threading machine and pipe. This helps prevent non-
operators from contacting the machine or pipe and
reduces the risk of tipping or entanglement.
10. Position the foot switch as shown in Figure 17, to allow
a proper operating position.
11. Check the level of RIDGID Thread Cutting Oil. Remove
the chip tray and oil pan liner; see that the filter screen
assembly is fully submerged in oil. See Oil System
Maintenance.
12. With the REV/OFF/FOR Switch in OFF position, run the
cord along a clear path. With dry hands, plug the
power cord into properly grounded outlet. Keep all
connections dry and off the ground. If the power cord is
not long enough use an extension cord that:
• Is in good condition.
• Has a three-prong plug like on the threading machine.
• Is rated for outdoor use and contains a W or W-A in
the cord designation (e.g. SOW).
• Has sufficient wire size. For extension cords up to 50'
(15.2 m) long use 16 AWG (1.5 mm
2
) or heavier. For
extension cords 50'-100' (15.2 m - 30.5 m) long
use 14 AWG (2.5 mm
2
) or heavier.
13. Check the threading machine for proper operation.
With hands clear of moving parts:
• Move the REV/OFF/FOR (2/0/1) Switch to the FOR
(1) position. Press and release the foot switch. Chuck
should rotate counter-clockwise when viewed from
the carriage end (see Figure 22). Repeat for REV
position – chuck should rotate clockwise. If the thread-
ing machine does not rotate in the correct direction,
or the foot switch does not control the machine
Machine and Work Area Set-Up
WARNING
Set up the Threading Machine and the work area
according to these procedures to reduce the risk of
injury from electric shock, machine tipping, entan-
glement, crushing and other causes, and to help
prevent threading machine damage.
Secure machine to stable stand or bench. Properly
support pipe. This will reduce the risk of falling
pipe, tipping and serious injury.
Do not use the Threading Machines without a prop-
erly operating foot switch. A foot switch provides
better control by letting you shut off the machine
motor by removing your foot.
1. Check work area for:
• Adequate lighting.
• Flammable liquids, vapors or dust that may ignite. If
present, do not work in area until source is identified,
removed or corrected, and area is completely ven-
tilated. The threading machine is not explosion
proof and can cause sparks.
• Clear, level, stable and dry place for all equipment
and operator.
• Good ventilation. Do not use extensively in small,
enclosed areas.
• Properly grounded electrical outlet of the correct
voltage. Check the machine serial plate for required
voltage. A three-prong or GFCI outlet may not be
properly grounded. If in doubt, have outlet inspected
by a licensed electrician.
2. Inspect the pipe to be threaded and associated fit-
tings. Determine the correct equipment for the job,
see Specifications. Do not use to thread anything oth -
er than straight stock. Do not thread pipe with fittings or
other attachments. This increases the risk of entan-
glement.
3. Transport equipment to work area. See Preparing
Machine for Transport for information.
4. Confirm equipment to be used has been properly in -
spected and assembled.
5. Confirm that the REV/OFF/FOR Switch is in the OFF
position.
6. Check that the correct dies are in the die head and are
properly set. If needed, install and/or adjust the dies in