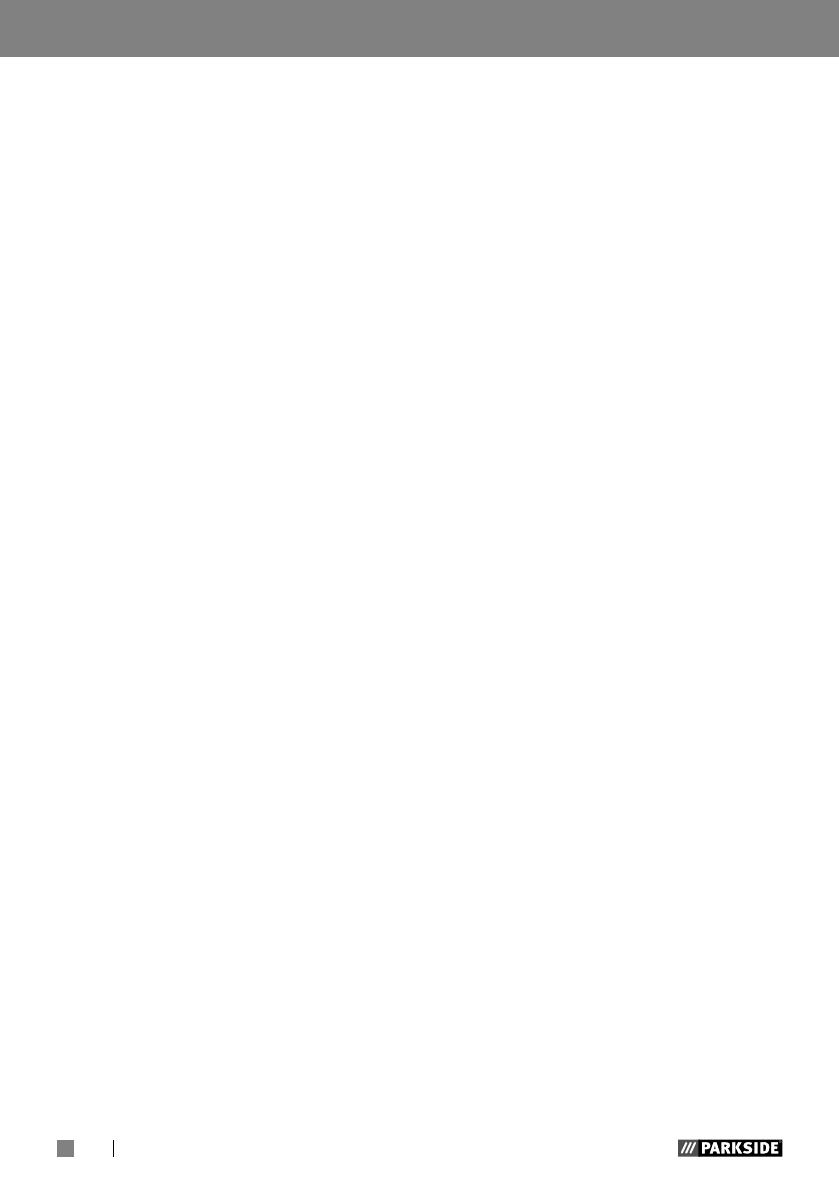
12 GB
z Operating hazards
When using the machine the
operator‘s hands may be ex-
posed to crushing, impact, cut,
abrasion and heat hazards.
Wear suitable gloves to protect
hands.
The operator and maintenance
personnel must be physically
capable to manage the weight
and power of the machine.
Hold the machine correct: be
prepared to counteract typical
or sudden movements – keep
both hands ready.
Be sure your body is well bal-
anced and maintain a solid
stance.
If tools are required to absorb
the reaction torque, use a sus-
pension attachment whenever
possible. If this is not possible,
we recommend side handles
for machines with straight han-
dle and pistol grip. At any rate
we recommend using tools to
absorb if it is greater than 4
Nm for machines with straight
handles, greater than 10 Nm
for machines with pistol grip
and greater than 60 Nm for
offset screwdrivers.
In the event of power failure
release the start- or stop con-
trol.
Only use the lubricants recom-
mended by the manufacturer.
Hex nut drivers with open flat-
head can crush fingers.
Do not use the tool in tight
spaces and be sure your
hands are not crushed be-
tween the machine and work
piece, especially when un-
screwing.
z Hazards due to repetitive
motions
When using a machine for
screw connections the oper-
ator may experience discom-
fort in hands, arms, shoulders,
neck or other body parts whilst
performing work-related tasks.
Maintain a comfortable posi-
tion whilst using this tool, be
mindful of a secure grip and
avoid awkward positions or
positions making it difficult to
maintain your balance. The
operator should change his
posture during extended pe-
riods of use, which may help
to prevent discomfort and fa-
tigue.
If the operator experiences
symptoms such as persistent
malaise, discomfort, palpita-
tions, pain, tingling, numb-
ness, a burning sensation or
stiffness, these warning signs
Safety instructions for air tools