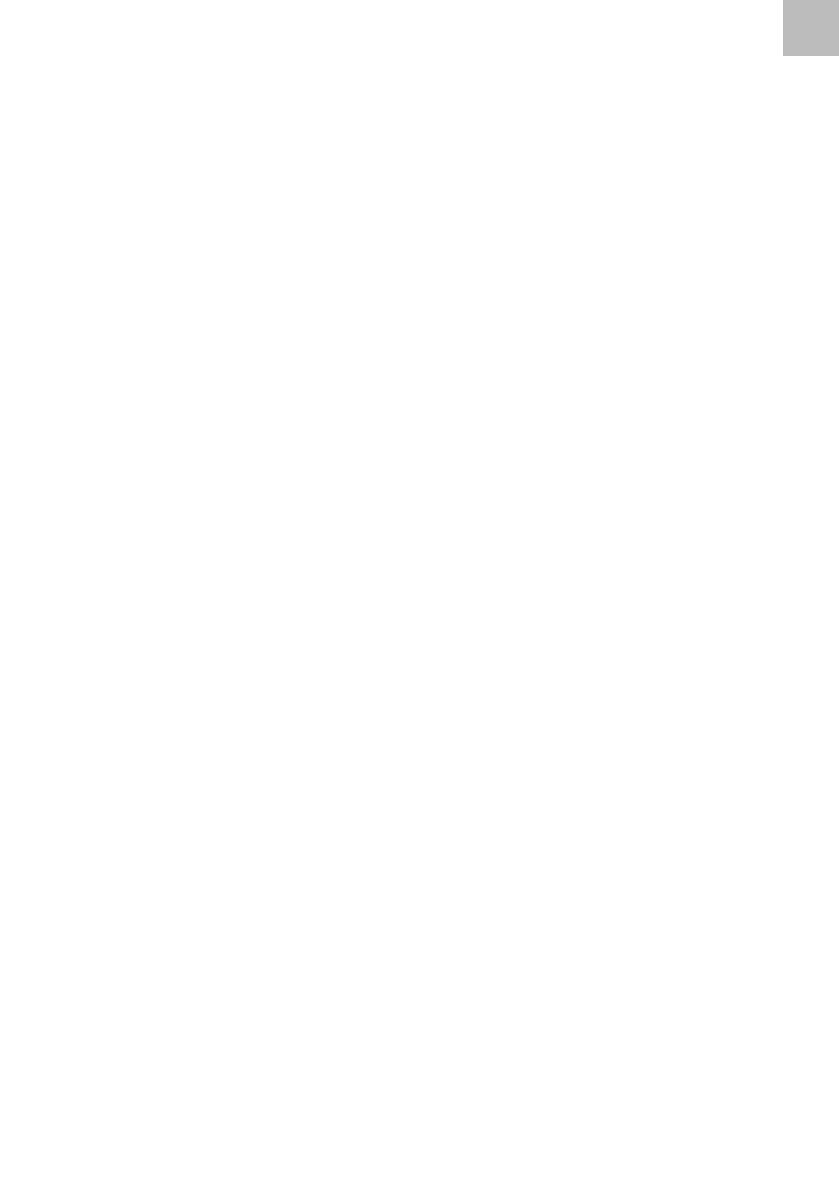
EN
EN - 12 EN - 13
2. Repairs of sealed components
2.1 During the repair of sealed components, all electrical supply must be
disconnected from the equipment being worked on before the sealed covers
are removed, etc. If it is absolutely necessary to have the equipment switched on
during service, then a continuously operating leak detector has to be placed in the
most critical location to warn of a potentially dangerous situation.
2.2 Special care must be taken to ensure that work on electrical components does
not alter the cover to such an extent as to affect the level of protection. This must
include damage to the cables, excessive number of connections and terminals
not made to the original specication, damage to the seals, incorrect design of
the seals, etc. It must be ensured that the device is installed securely. It must
be ensured that the seals or sealing materials are not degraded in such a way
that they no longer serve the purpose of preventing the entering of ammable
materials. Spare parts must comply with the manufacturer's specication. The use
of a silicone seal may suppress the effectiveness of some types of leak detection
devices. Internally safe components do not have to be disconnected before they
can be worked on.
3. Repairs of internal safe components
No permanent inductive or capacitive loads shall be applied to the circuit without
ensuring that the permissible voltage and current permitted for the equipment used
are not exceeded.
Internally safe components are the only types that can be worked on in a ammable
environment, even if they are live. The test equipment must be correctly dimensioned.
Parts are replaced only by parts specied by the manufacturer. Other parts may ignite
the refrigerant if it leaks into the environment.
4. Wiring
Check that the wiring is not exposed to wear, corrosion, excessive pressure, vibration,
sharp edges or any other adverse environmental effects. The inspection must also
take into account the effects of aging or permanent vibrations from sources such as
compressors or fans.
5. Detection of ammable refrigerants
Under no circumstances may potential sources of ignition be used to search for or
detect refrigerant leaks. The halogen burner (or any other detector using open ame)
must not be used.
6. Leak detection methods
The following leak detection methods are considered acceptable for systems contain-
ing ammable refrigerants.
Electronic leak detectors must be used to detect ammable refrigerants, but their sen-
sitivity may not be adequate or may require recalibration. (The detection device must
be calibrated in a refrigerant-free space). It must be ensured that the detector is not a
potential source of ignition and is suitable for the refrigerant used. The leak detection
device must be set to the percentage of LFL refrigerant and must be calibrated to the
refrigerant used and the appropriate gas percentage (maximum 25%) conrmed.
Leak detection uids are suitable for use with most refrigerants, but the use of chlo-
rine-containing detergents must be avoided because chlorine can react with the
refrigerant and corrode copper piping.
If a leak is suspected, all open res must be eliminated / extinguished.
If a refrigerant leak is found, which requires brazing; all refrigerant must be removed